The ordinary individual does not generally come into contact with gas turbines. However, if your job is in the aviation, railway, or ship manufacturing industries, you may come into contact with gas turbines regularly. Gas turbines are also utilized to manufacture gas compressors, generators, pumps, and tanks. This machinery is costly and has a high operational cost of approximately $16.00 per mmBTU (One Million British thermal units).
Individuals who operate this type of machinery understand the importance of adequate air filtration for gas turbines. They also understand the impact on the efficiency of the entire machine, hence the business. Additionally, if the airflow for a turbine system is correctly filtered utilizing High-Efficiency air filters, they can realize reduced monthly maintenance expenses. In addition, the performance of the compressor will considerably improve with effective air filtering. Finally, the use of high-quality HEPA filters can optimize clean operations, reduce shutdowns, and reduce the frequency of technical inspections.
If you are unfamiliar with gas turbines and how they operate, keep reading.
What Exactly are Gas Turbines?
Sometimes known as a combustion turbine, a gas turbine is a continuous internal combustion engine. Turbines generate mechanical energy from natural gas or other liquid fuels. This energy then powers a generator, which generates electrical energy, such as that which flows through power lines to our businesses and homes. Gas turbines are highly efficient and serve as the engine at the core of a power plant that generates electric currents. Once generated, electricity is utilized to power a mechanical process or source. The following are the major components shared by all gas turbine engines:
- Rotating gas compressor located upstream
- Combustor
- Downstream turbine connected to the shaft the compressor is on
- A fourth component is frequently employed to improve efficiency (on turboprops and turbofans), transfer power to mechanical or electrical form (on turboshafts and electric generators), or obtain a higher thrust-to-weight ratio (on afterburning engines).
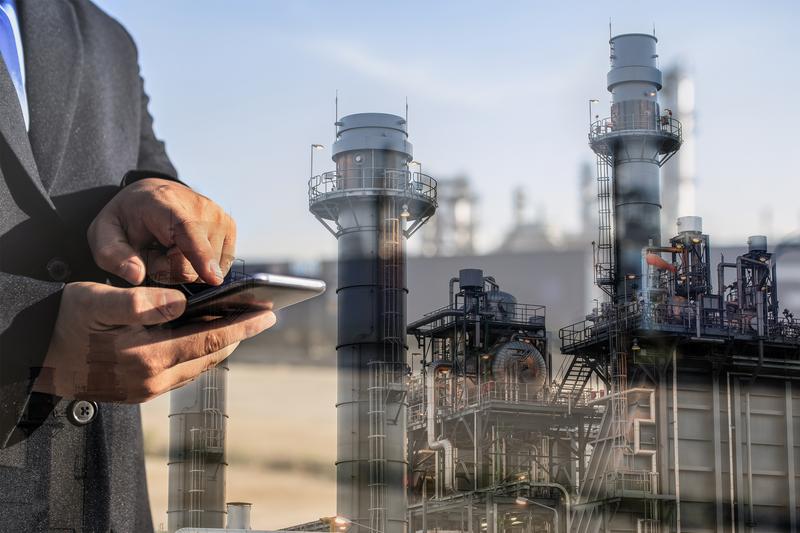
How Do Gas Turbines Operate?
The basic operation of a gas turbine is a Brayton cycle with air as the working fluid: atmospheric air flows through the compressor, increasing its pressure; energy is then added by spraying fuel into the air and igniting it, producing a high-temperature pressurized flow; this high-temperature pressurized gas enters a turbine, producing shaft work output, which is used to drive the compressor; the unused energy escapes in the exhaust gases. The gas turbine’s function dictates the design to obtain the most desired energy split between thrust and shaft work. Because gas turbines are open systems that do not reuse the same air, the fourth phase of the Brayton cycle (cooling of the working fluid) is omitted.
Gas turbines power airplanes, electrical generators, gas compressors, pumps, ships, tanks, and trains.
To better understand how a gas turbine works, below are the basics.
- Compressed air is first combined with fuel. Then, the combination of air and fuel ignites instantly, burning at a very high temperature, which produces a hot gas.
- The gas that is created drives the blades of the turbine to spin.
- The spinning blades cause the turbine’s driving shaft to turn.
- The turbine is connected to a generator rod, which spins a big magnet encircled by copper wire coils. The turbine’s rotation powers the generator.
- The rotating generator magnet generates a magnetic field, forcing electrons to line up and flow around the copper coils. The flow of electrons through wire results in the generation of electricity.
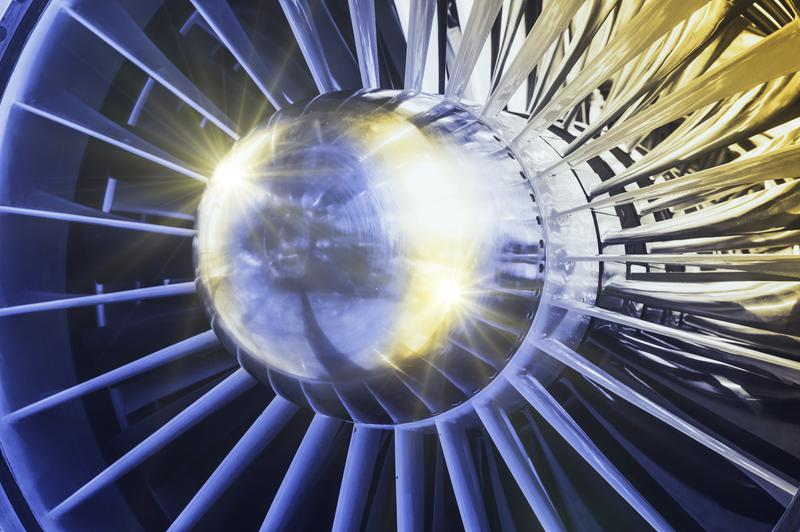
Gas Turbine Air Filters
As previously stated, adequate filtration is critical to a gas turbine’s overall performance. If particulate matter gets inside your machinery, it can cause fouling. This is when a build-up of particles on the compressor blades occur, which can cause erosion, or corrosion over time. In addition, a gas turbine will consume around 4,300 metric tons of air, consisting of approximately 98 percent air and 2 percent fuel on a typical day. Therefore, it is vital to invest in high-quality air filtration to help prevent the turbine from experiencing excessive damage.
Concerning filtration, the primary focus is to use filters that fulfill the most stringent burst strength and particle filtering efficiency standards. In addition, the appropriate filter should be based on the project’s environmental conditions and pollutants.
There are two types of gas turbine filtration systems: pulse filtration and static filtration. Pulse filters are thought to be “self-cleaning.” The main distinction between the two is the environment in which they operate.
Suppose the region in which you are operating has a dust particle concentration that is more than 0.300 mg/m3, or there are regular sandstorms. In that case, a pulse filtration system is recommended over a static system. However, the environment and operational circumstances might change. Therefore, it is essential to tailor the filter solution you select to your specific environment and the needs of the business.
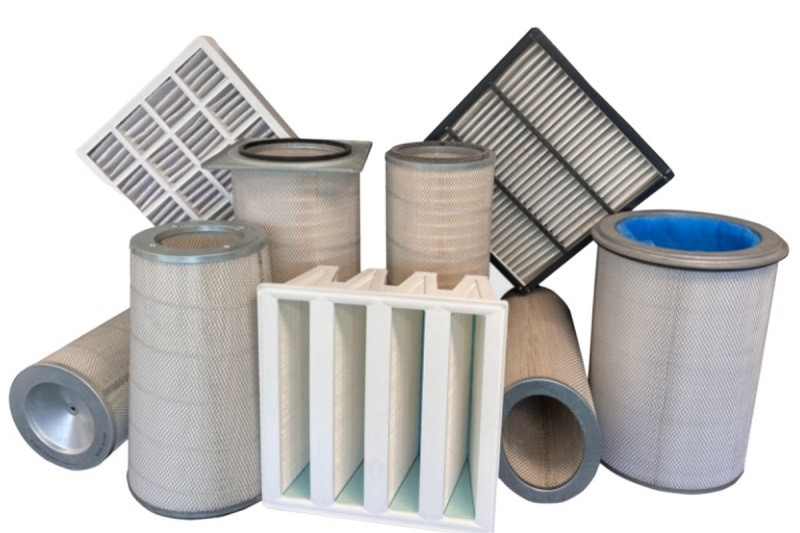
Gas Turbine Pulse Filters
Pulse filters are the preferred choice for dusty and snowy situations. Cement factories, steel mills, and refineries are examples of businesses that might need pulse filters for their gas turbines. In addition, pulse filters are often used in regions like Africa and the Middle East because of the abundance of sand and dust storms. These systems effectively prevent filter blockage caused by sand, moisture, and other contaminants.
Pulse filter systems are very efficient since they may be cleaned when they are not in use. This allows for uninterrupted operations since your equipment is automatically cleaned between usage.
Gas Turbine Static Filters
Static filters are a less expensive and easier-to-maintain solution if there isn’t a need to filter large particles such as sand. In addition, most static filter systems have pre-filters that you can easily clean or replace. Likewise, they are reasonably priced, but can quickly add up in the long run.
Gas Turbine Bag Filters
Bag filters are primarily utilized in the gas turbine air inlet as pre-filters. They eliminate coarse pollutants and act as a coalescer to remove small water droplets in the air stream. Because the bag filter is made to handle excessive humidity, high velocity, and turbulence, it is ideal for air handling systems.
Mini-Pleat Filters
Mini-pleat air inlet filters are high-efficiency filters used for second and or third stage filtering in gas turbine air inlet systems. The box-type compact filters have robust construction, high efficiency, and minimal pressure drop. This makes them a reliable and cost-effective alternative for turbomachinery in harsh, humid situations. Mini-pleat filters tolerate humidity, high velocities, and turbulence encountered in both ambient and process environments.
Cartridge Filters for Gas Turbines
Cartridge filters, both static and self-cleaning pulse, are offered in vertical or horizontal configurations to fit your system’s needs. Canister and cartridge filters are utilized on and offshore in supply air systems for gas turbines and turbo compressors.
Panel Filters for Gas Turbines
Panel filters are commonly used as pre-filters in gas turbine static inlet systems. The primary function of pre-filters is to eliminate large particles like pollen and other gritty pollutants and droplets of water. Graduated denier polyester fibers with an upstream layer of larger fibers followed by denser, finer fibers for increased loading and dust holding capability provide longer life.

Doing Our Part for Cleaner Air
Filters are an essential component of gas turbines because they remove pollutants from the fuel before it is burned. This increases the turbine’s efficiency and minimizes the chance of damage to the turbine blades. Filters also serve to increase the life of gas turbines by preserving the moving parts from wear and tear. As a result, frequent maintenance and relacing filters for gas turbine are necessary to ensure peak performance. With over 45 years of trusted experience in the filtration industry, Braden Filtration is an industry leader in Filtration. We manufacture high-quality, durable, and long-lasting filters to meet your business needs. For more information on filtration products for gas turbines, contact Braden Filtration.
Comments are closed